Mastering the Art of Baking Modeling Clay: A Detailed Guide
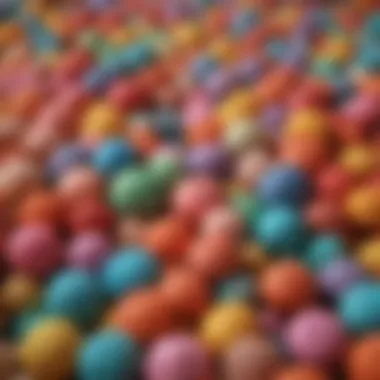
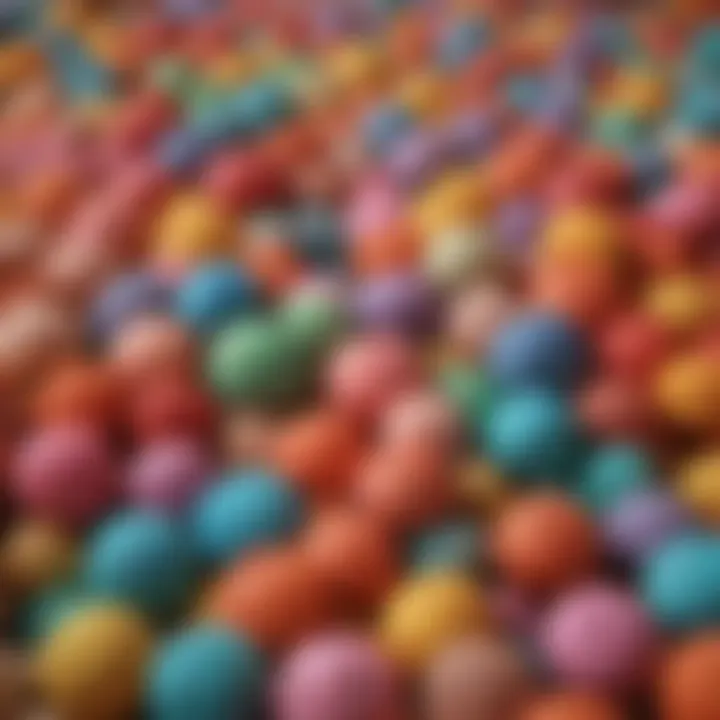
Intro
Baking modeling clay is critical for crafters who want their work to have permanence. This process can seem daunting to some, yet its procedures are quite clear-cut when broken down effectively. In this guide, we will examine each component of baking modeling clay, providing a roadmap from preparation to the baked product.
We will look into materials needed, proper techniques to ensure optimal results, essential safety precautions, and ways to troubleshoot common issues. The aim is to equip both amateurs and seasoned creators with the critical skills for successful baking. Through thoughtful preparation and careful execution, ensuring the lasting beauty of your creations becomes an achievable desire.
Recipe Overview
- Creative Name: The Art of Baked Clay Creations
- Yield: Dependent on the size of your clay project
- Preparation Time: About 15 to 30 minutes
- Baking Time: Typically, 30 minutes to 1 hour
- Skill Level: Medium
- Main Ingredients:
- Polymer clay (like Sculpey or Fimo)
- Tools for shaping and cutting
- Oven (traditional for baking)
Key Points to Discuss
Our exploration into this topic will detail:
- Necessary materials for baking modeling clay.
- The step-by-step procedures to ensure successful baking.
- Tips to troubleshoot any challenges that may arise.
- Safety guidelines to consider during the baking process.
By bestowing knowledge on these aspects, crafting enthusiasts can confidently approach their projects. We commence the guide with detailed step-by-step instructions that ensure users engage fully with the baking process.
Prologue to Baking Modeling Clay
Baking modeling clay is a pivotal step in creating craft projects that stand the trial of time. When enthusiasts engage in projects using this unique medium, understanding the nuances of baking not only enhances the quality of their creations but also provides a foundation for experimentation and skill development.
Understanding Modeling Clay Types
There are various types of modeling clay available on the market, and each serves a specific purpose. Polymer clays like Sculpey and Fimo are popular for their flexibility and vibrant colors. These clays require baking to harden, making them excellent for detailed sculptures and intricate designs. Comparatively, natural clays, including air-dry varieties, do not require any form of heating but often necessitate extra care in handling due to their water-based components.
Selecting the right type of clay is fundamental for achieving desired results in baking. Different clays have distinct baking requirements in terms of temperature and duration, which can significantly affect the final product. Crafting enthusiasts must invest time to grasp the features of each clay type, as their choice will greatly influence both the process and the outcome.
Importance of Baking in the Crafting Process
Baking is not merely a step; it is the capstone of a multi-faceted crafting process. Thorough baking transforms soft and pliable clay into robust figures that can sustain wear, making their creations viable for both practical use and display. Properly hardened pieces exhibit improved durability against elements, wear, and even breaking.
The advantages of baking modeling clay include:
- Enhanced Strength: Solidifying the creation allows it to endure handling and usage.
- Detail Retention: Quality baking ensures that the fine details artists have implored are preserved.
- Varied Techniques: Understanding baking also opens the door to explore mixing clay types, paints, and sealants effectively for unique aesthetics.
Moreover, baking allows for customization. Using varying temperatures can yield different effects and textures, providing creative freedom. Therefore, a conscious focus on the baking aspect contributes immensely to the artistic journey.
Proper baking practices can elevate a simple project into a statement by transforming fragile installations into lasting art pieces.
Materials Required for Baking Modeling Clay
When engaging in the process of baking modeling clay, one must understand the essential materials that will ensure optimal results. Each material plays a crucial part in the crafting experience. The correct modeling clay will exhibit desired characteristics under heat, while appropriate tools will facilitate a controlled baking environment. Understanding these elements not only enhances the crafting process but also ensures that finished pieces are durable and well-preserved.
Choosing the Right Modeling Clay
Selecting the right modeling clay is fundamental. There are variations such as polymer clay and air-dry clay, each offering unique properties. For instance, polymer clay hardens through baking at specific temperatures, making it ideal for pieces intended to last. Air-dry clay, on the other hand, doesn't require an oven and dries at room temperature. When choosing, consider the project’s durability needs. Selecting high-quality clay ensures that your effort comes to fruition in a satisfying, enduring creation.
Baking Tools and Equipment
To precisely manipulate and control the baking process, a few tools are essential. The following subsections discuss each key component.
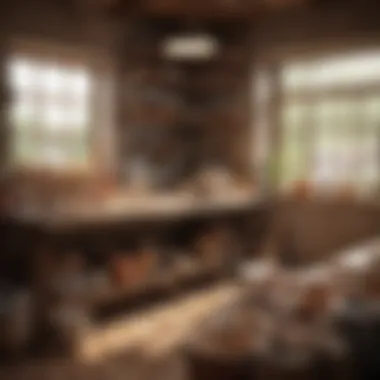
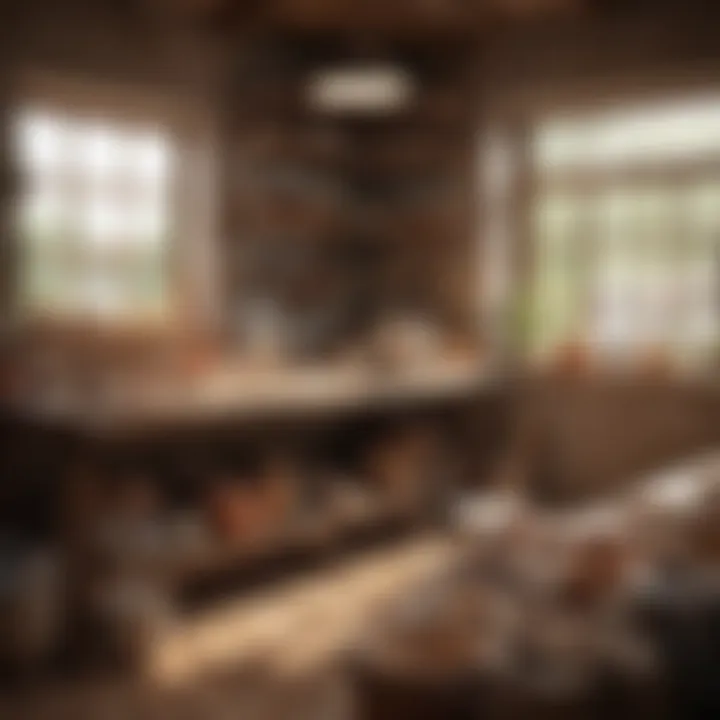
Standard Oven
A standard oven is critical for baking modeling clay to achieve solid and completed works. Its capacity to maintain steady temperatures enhances uniform baking. Most home kitchens have this essential appliance. It can reach needed baking temperatures quickly and proficiently.
One significant characteristic of standard ovens is their heated airflow which aids in achieving the desired consistency in baked clay. Users can benefit from an electric or gas oven, with both offering reliable results but varying in preheat times and heat distribution. It is advisable to avoid microwave baking, as it often results in uneven curing.
Baking Sheets
Baking sheets serve as a foundation for your creations during the baking process. This tool allows the warm air to circulate evenly around items, reducing the chances of unintended adhesion to surfaces. Generally, using non-stick sheets further minimizes mess during the baking.
Baking sheets can differ in materials. Some are aluminum, while others are insulated options. An insulated baking sheet is known for preventing burning of the edges of the clay. Alternating layers or perforated and solid baking sheets can play an essential role in optimizing the process and adapting for various types of projects.
Aluminum Foil or Parchment Paper
Aluminum foil or parchment paper acts as a barrier between baked pieces and the baking surface. By using this approach, there is less risk of damaging your clay as it bakes. Both materials also help in easier cleanup after baking. Parchment paper is heat-resistant, and it reduces the likelihood of sticking that might warp details of sculptures or crafts.
A key feature of parchment paper is its reusable nature when properly cared for. This quality can help reduce material costs over time. Aluminum foil, while generally less inflexible, offers easy shaping around intricate pieces but may leave impressions if too tightly formed.
Thermometer
Using a thermometer ensures the baking is done at the proper temperature and can prevent unintended destruction of delicate works. An oven thermometer is handy for receiving accurate readings. By cross-referencing the internal temperature of the oven, adjustments can be made if needed.
A distinctive aspect of thermometers is their ease of use and visibility. Most are straightforward and can be placed within the oven, showing temperatures accurately as it bakes. Ensuring the correct temperature throughout the baking provides assurance in the final resilience of creations. A temperature discrepancy can negatively affect the baking frequency. As a resource for enthusiasts, this supplemental tool promises quality and consistency.
Understand that each material or tool discusses plays a pivotal role in how well your modeling clay fares during the baking process.
Preparing Your Clay for Baking
Preparing your modeling clay adequately is crucial to the success of your final creation. This phase involves various strategies to ensure you develop your artwork in a way that's conducive to effective baking. By focusing on shaping and detailing your clay, as well as setting up your workspace, you enhance the quality and durability of your end product. It lays a strong foundation for what follows, making all subsequent steps more efficient and yielding better results.
Shaping and Detailing Your Creation
Shaping your modeling clay is an art form in itself. You can mold it into a variety of forms depending on your project. Proper shaping influences how well the clay bakes and perhaps more importantly, how it holds its intended shape post-baking.
Consider the following aspects:
- Purpose of the Creation: Understand what you want to achieve. This may dictate your shaping methods or techniques. Whether sculpting an intricate figure or a simple ornament, clarity of purpose sharpens focus.
- Tools for Shaping: Use specific tools that cater to your needs. These may include various knives, sculpting tools, or even household utensils that help create textures.
- Detail Precision: Pay attention to the details. Small features can significantly affect overall appearance and will be pronounced when baked. Aim for the right texture and clarity when detailing.
The motivation by which you shape the clay can make or break your work; every groove and curve should serve a projected vision for your creation. Watching your creation take form is rewarding.
Setting Up the Workspace
Having an efficient workspace enhances productivity and minimizes issues during the preparation phase. A well-thought-out space can maintain focus and ensure your comfort, ultimately culminating in a better-crafted piece.
Key Writing Considerations:
- Clean and Organized: A clean surface is pivotal. Remove unnecessary items and gather only essential tools and materials that you will use for the current project.
- Lighting: Ample lighting is very useful. Good visibility allows you to see the details you missed can significantly improve your ability to spot imperfections.
- Temperature Adaptations: Ensure the environment you work in is comfortable, avoiding overly cold conditions that may harden your clay prematurely.
By adhering to these centered preparations, you can deepen your engagement with the crafting process leading to favorable outcomes.
Preparing carefully sets the standard for your final product, paving the way for an enjoyable baking experience.
The elements outlined above, whether it be surrounding yourself with the right tools or modifying conditions to suit your needs, are all geared toward optimizing your preparation. The effort you invest will unveil the true capability of your modeling clay throughout the tutorial process.
Baking Methodology
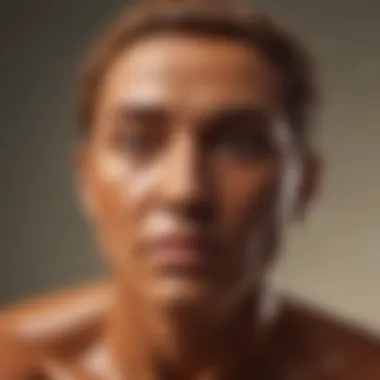
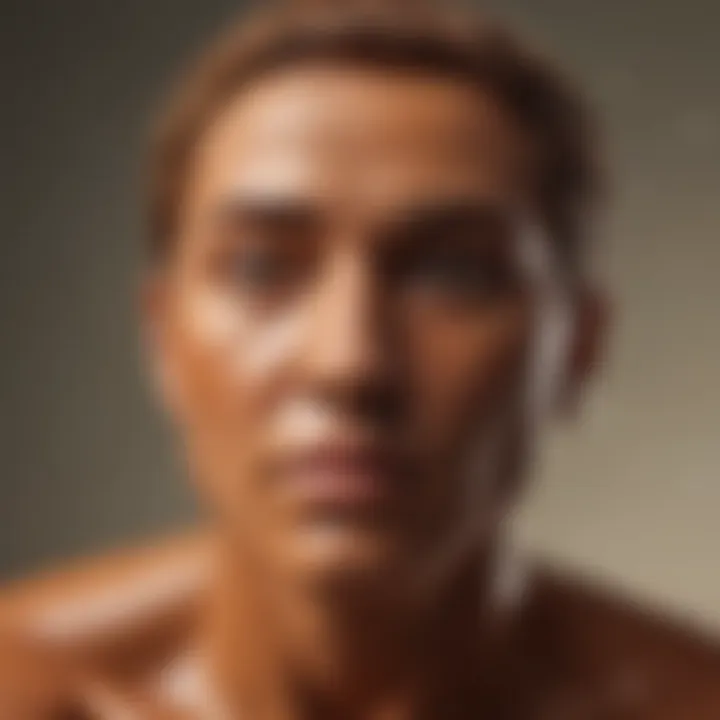
Baking modeling clay is a crucial aspect of creating durable and lasting artistic pieces. This methodology is not just about heat and time; it involves precise actions that dictate the success of your creation. In this section, we delve into the specific elements of the baking process. Understanding them is essential for achieving optimal results with your modeling clay.
These steps ensure that your work does not just appear finished but is solidified into a lasting form. Proper baking enhances the characteristics of the clay while preventing common troubles like cracking. These methodologies provide both reassurance and confidence in crafting pieces that withstand the passage of time.
Preheating the Oven
Before you begin baking your modeling clay, preheating the oven is vital. This step ensures that the clay starts to set properly as soon as it is placed inside. Most modeling clay products recommend an initial temperature. Typical values range from 265°F to 300°F, varying by brand. Check the packaging of your clay for exact instructions.
When preheating, allow for a full heating cycle. This can typically take around 10 to 15 minutes. A divided or uneven temperature may lead to uneven baking. To measure the appliance's temperature accurately, you can use an oven thermometer. This stops heat variations that could affect the final results of your work.
Baking Temperature Guidelines
Correct baking temperature is paramount. Each type of modeling clay requires a specific setting. Using temperature inappropriate to the type may lead to undesired changes. Examples vary significantly between brands like Sculpey, Fimo, or Premo. For most clays, temperatures lie between:
- Sculpey III: 275°F
- Fimo Soft: 230°F
It is wise to avoid temperatures exceeding the manufacturer’s recommendations. Too high of a setting can cause your clay to brown or even burn. Therefore, always adhere strictly to the baking instructions to maintain color and texture. Checking the brand's specifications ensures that the baking process comes as beneficial rather than detrimental.
Recommended Baking Time
Baking time can differ, concerning the thickness, size, and brand of your clay project. Generally, thinner pieces bake relatively quicker, while larger or denser items need longer exposure to heat. As a guideline, for thinner elements, about 15 minutes can suffice, whereas thicker items might require as much as 30 minutes.
To avoid potential artifacts linked with overbaking, larger items or complex structures warrant more attention. A recommended method is:
- Start with the shorter time frame. Track your clay as it bakes.
- Check for hardness: The piece should not feel soft or malleable.
- If necessary, add incremental time, ten minutes at a time.
Refer to your specific brand for tailored suggestions. Follow these guidelines effectively to encourage successful and reassuring baking experiences.
Safety Precautions While Baking
Baking modeling clay can be an enjoyable and rewarding process. However, with this activity comes specific risks that require consideration. Embracing safety precautions helps prevent accidents and ensures a smoother crafting experience. Being meticulous about safety during the baking process not only protects your physical well-being but also safeguards your creative projects.
Safe Handling of Hot Materials
Engagement with hot materials is inherent to the baking of modeling clay. Understanding how to manage these elements is crucial. Urling implements like gloves, hot pads, or oven mitts can mitigate risks associated with direct contact. Moreover, equip yourself with tools that minimize the chance of dropping or spilling creations.
When removing baked clay from the oven, take vital care. Open the oven slowly to avoid coming into contact with heat. Hold the tray firmly but do not grip it too tightly as it may cause slips. Always use a thermometer that checks the absorption temperature for modeling clay, preventing dangerous reactions.
Remember: Always work on a non-flammable surface to limit hazards further.
Ensuring Proper Ventilation
Ventilation plays a critical role in ensuring a safe baking process. Oftentimes, the substances used in modeling clays can release fumes when baked, even though many brands advise their safety. To maintain a secure environment, ensure your workspace is sufficiently ventilated. Open a window or turn on a fan to allow fresh air flow. This will not only remove any fumes but will also maintain an optimal baking milieu.
If possible, bake in a space where the air quality can be easily assessed. Never leave baking clay unattended, especially in confined spaces. Preemptively monitoring temperatures at all times will also ensure your safety and the integrity of your finished product.
By adhering to these precautions, the risks involved in baking modeling clay can be greatly reduced, allowing for an enriching experience that focuses on creativity rather than worry.
Post-Baking Process
The post-baking process is a crucial phase in working with modeling clay. This stage plays a significant role in ensuring that the final piece achieves the desired quality and longevity. Proper handling and evaluation after baking is vital. It provides an opportunity to assess the work, ensuring that no steps were missed in the crafting process. The present section outlines the necessary steps for confirming the completeness of the baked piece and explains the importance of allowing your creation to cool adequately.
Checking for Completeness
After your piece has finished baking, it is essential to evaluate it closely. Just like when cooking, some aspects may not be noticeable right away, but could impact the final integrity of the object. Check for
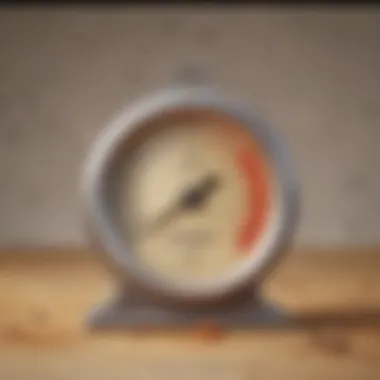
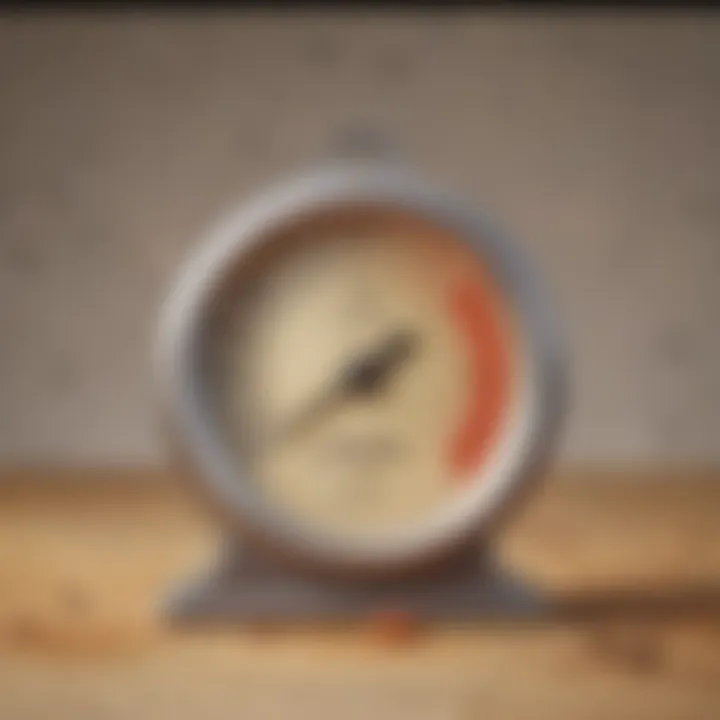
- Structural soundness: Confirm that there are no fragile areas or sections that seem compromised due to the heat.
- Consistent color: Ensure the desired color is achieved uniformly; uneven baking can lead to visible patches.
- Overall appearance: Look for imperfections, like cracks or flaws that are not consistent with your intended design. If defects exist, it might require additional attention or a redo.
To accurately assess completeness, consider using a fine-tipped tool to gently poke or prod at areas that seem weaker. If you notice soft areas, they may indicate that additional baking was required. A visual approval can save you from complications down the line.
Always allow yourself a moment to evaluate your final product thoroughly. This step often separates well-crafted pieces from those that fall short of expectations.
Cooling Down Your Creation
Cooling is an essential phase in the post-baking process, impacting not only the final appearance, but also the durability of the piece. This practice involves more than simply letting it sit. Allow the creation to cool
- In a safe location: Move your creation to a flat, heat-resistant surface. Avoid placing it on cold materials like tile or metal surfaces that can cause stress cracks due to rapid temperature changes.
- At room temperature: It is best to allow the clay to return to room temperature naturally. This gradual cooling will help avoid thermal shock.
Waiting to manipulate your item serves not only to preserve the finish but also safeguards the structure. Handle it with strict care until it achieves firmness at ambient temperatures, as sudden movements could lead to damage. Patience here directly enhances the craft's overall quality and your satisfaction with the result.
Common Issues and Troubleshooting
Baking modeling clay is not an impeccable process. While many practitioners succeed seamlessly, others might encounter challenges. Identifying common issues and know how to troubleshoot them is vital for achieving satisfactory results. Ignoring problems can lead to disappointing outcomes or hazards in the crafting process. Therefore, this section presents significant aspects to address during and after baking, provided with clear solutions.
Dealing with Cracks and Imperfections
Cracking in modeling clay can result from several factors, notably the baking temperature and the thickness of your creation. When the temperature is too high or if the object is very thick, it may dry too quickly, causing cracks. Here are some steps to manage and prevent cracks:
- Control Thickness: Try to maintain a uniform thickness across your piece. Thicker areas absorb heat differently, leading to stress and resulting cracks.
- Lower Baking Temperature: If you experience regular cracking, consider reducing the temperature and baking for a longer duration. This slow process helps ensure even heating.
- Smooth Surface: Before baking, gently smooth the surface of your work. This measure can help prevent cracks appearing post baking.
If you already notice cracks in your finished products,
- Use a strong glue to carefully fill gaps, then sand the area once dry, allowing it to seamlessly blend back into the piece.
- Paint over imperfections to disguise them and create a visually appealing aspect in your artwork.
Addressing Color Changes
Changing colors is a frequent issue that can occur when baking modeling clay. Variables could include the type of clay, the baking process, or even the color itself. Certain hues may change depending on heating intensity or the duration of exposure.
To handle undesirable color shifts, consider:
- Utilizing Correct Temperature: Always follow the recommended temperature settings for the specific modeling clay brand being used.
- Experiment with Test Pieces: Before launching into larger projects, test small pieces. This helps you to see how they react under particular conditions.
- Add a Clear Coat: After the baking process, consider applying a clear seal. This treatment can preserve both texture and color.
Identifying and Resolving Incomplete Baking
Sometimes, despite strict adherence to temperature settings and timing, your sculpted art may still appear soft or not fully set. Incomplete baking can arise from several factors, such as insufficient time in the oven or uneven heat distribution.
To rectify this, examine these options:
- Thermometer Usage: Employ a reliable oven thermometer. Depending on the oven type, temperatures may vary, affecting consistency in the baking process.
- Visible Checks: After the designated time, lightly touch the surface. It should feel firm; if not, place it back in the oven for additional time while monitoring accordingly.
- Avoid Over Resetting: While ensuring full baking, continually examin it. You want to dodge excessively heating, which leads back to crackant problems.
Remember: Regularly monitoring your work in the oven aids in achieving the optimal texture and consistency.
Knowing how to troubleshoot common issues elevates your baking experience. It empowers crafters to refine and excel in their modeling clay projects.
Final Thoughts
Baking your modeling clay is a significant process that transcends mere crafting; it transforms your creations into tangible art pieces. In this guide, we discussed several factors crucial to achieving the best results, from choosing the right materials to ensuring proper baking conditions. Understanding these key elements plays a vital role in getting the most out of your crafting experience.
Encouraging experimentation stands as a cornerstone of artistic growth. When you step outside of typical crafting routines and allow yourself to explore, your work greatly improves. Each baking process is a lesson, opening avenues for creativity and problem-solving. Recognize that outcomes are often unpredictable, and within that unpredictability lies a chance for innovation.
Moreover, gaining practical knowledge empowers you to tackle any potential pitfalls in your crafting journey, helping you to precisely identify and refine your process. Recognizing the common issues and how to solve them builds confidence. Your very hands become skilled tools capable of bringing visions to life.
Resources available for further learning can enhance the skills developed through this guide. Whether through forums like Reddit or educational platforms like Britannica, you will find a wealth of information. Ultimately, interpreting the information with a mind geared for continuous learning allows for self-improvement. In the end, the deepest understanding is forged through personal endeavor and experience.
Plunge yourself into the vibrant possibilities of crafting, and let each bake become a step toward your artistic mastery.
Grasping these elements ensures consistency and confidence as you continue your journey with modeling clay. Now, embrace the potential hidden within and enjoy the rewarding process of crafting.